New year, new Alberta OHS requirements. Are you ready?
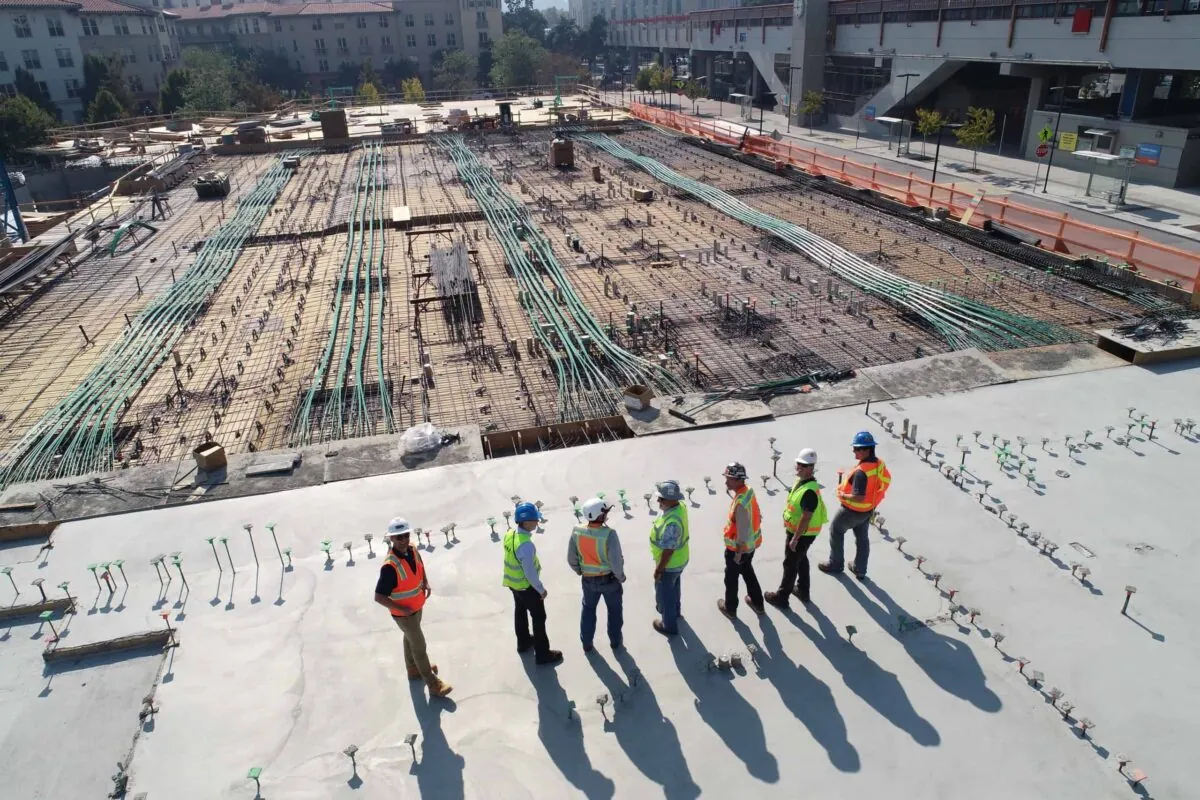
Authors: Aaron Marchadour, Reagan Munro, John Agioritis
The Government of Alberta recently announced that a number of changes to the province’s Occupational Health and Safety (OHS) Code will come into effect on March 31, 2023.
As required under the OHS Act, the province publishes three-year OHS Code review plans to ensure the Code is up to date. These latest changes reflect current health and safety best practices, remove duplication, reduce administrative burden and align the OHS Code with the OHS legislation in other provinces.
Here are some of the key changes that will take effect this year.
First aid requirements
- Prior to sending any workers to the work site, prime contractors or employers will be required to implement a plan to transport ill or injured workers from the work site to the nearest healthcare facility. These plans must be implemented prior to March 31, 2023, to ensure uninterrupted work at the work site.
- Prime contractors and employers should review the updated tables attached to the OHS Code identifying medium-hazard work and high-hazard work and ensure workers designated as first aiders have the required training.
- Where required, advanced first aiders will need to be positioned near the first aid room and readily available for workers. Their duties will need to allow them to remain in a fit and clean condition to conduct first-aid duties.
- Prime contractors and employers that currently stock Alberta Type P, No. 2 or No. 3 first aid kits should review the new first aid kit standard that applies to their worksite and ensure they add any additional items to their kits.
Mining
- Employers will be responsible for ensuring that any mine plan is reviewed and updated at reasonably practicable intervals.
- Excavation boundaries will be adjusted “to ensure safe distances are maintained” rather than the previously prescribed distances of 10, 20 and 30 metres.
Oil and gas wells
- Prime contractors or employers will be responsible for providing site-specific orientation to workers prior to workers entering the worksite for the first time. The orientation must include information on site-specific hazards, work procedures that must be followed, an emergency response plan, processes for reporting hazards and other important information as identified in the OHS Code.
- An employer that rents or leases equipment must make reports of all inspections and repairs done on the rented or leased equipment and provide them to the supplier.
- The previous seven-day inspection requirement attached to drilling rigs, service rigs, snubbing units, swabbing units and other well-servicing or drilling equipment will be updated to “reasonably practicable intervals” for as long as the equipment is in service.
Managing control of hazardous energy
- Workers will be permitted to perform work on a machine while it is operating as long as the machine has been “otherwise made safe.” This will allow workers greater flexibility in cases where equipment that needs to continue operating can be made safe to work on.
- Employers will be responsible for providing personal locks to workers who are involved in isolating hazardous energy. The employer will need to create and maintain a list of workers and a description of their lock. In cases where a lock may be transferred, the employer will be solely responsible for the transfer.
- Employers will be required to develop and implement group control procedures if individual workers would be unable to provide adequate protection. The employer will be responsible for designating a worker or supervisor to fulfil tasks set out in the OHS Code.
- In the event that securing by individual or group workers is inadequate, employers will be required to develop complex group control procedures that must be certified by a professional engineer as safe and appropriate for the protection of workers.
Updated technical standards
- Technical standards for various work site equipment, machinery, training and safety assessments have been updated to reflect industry best practices. Employers must ensure their policies align with the updated Canadian Standards Association standards.
Confined spaces
- Employers will no longer need to receive approval to use a remote confined space entry monitoring station at a work site.
- Remote monitoring stations will need to comply with the minimum standards set out in the OHS Code, including being physically located at the same work site as the confined space and having a live visual display that allows the monitoring worker to have a clear view of the confined space where a worker may be.
Noise
- The threshold for conducting a noise exposure assessment will be moved from 85 dBA to 82 dBA to ensure noise levels are assessed prior to exceeding the occupational noise level.
- Noise assessors will need to be trained in conducting noise exposure assessments and calibrating, operating and maintaining noise assessment equipment. They must be able to demonstrate an understanding of the method being used for measuring noise exposure.
- Employers’ records of noise assessments must include a list of all of the tasks the assessor observed a worker perform. Employers will only need to retain a record of noise assessment for three years. For many employers, this will be a reduction from the previous standard.
Overhead power lines and electrical utility workers
- Employers will be required to notify the applicable electric utility, rural electrification association or industrial power producer of an overhead power line prior to any work being done or equipment being operated near it.
- Employers and workers will be required to assume and operate as if all overhead power lines are energized at all times.
Explosives
- Blaster’s certificates (previously called blaster’s permits) will no longer expire after five An Alberta OHS director may still suspend or cancel a blaster’s certificate but need not provide a written reason for doing so.
- If a blaster’s certificate is suspended or cancelled, it will no longer result in the automatic suspension of all other blaster’s certificates related to that work site.
- Blasters will be required to report all suspected, attempted or known instances of theft of explosives to their employer, who will then be responsible for reporting the loss or theft to police.
- Employers and blasters will be responsible for ensuring that there are no adverse weather conditions that may detonate an explosive or create a hazard to workers. If an adverse weather condition exists, all blasting must be stopped and workers must be moved to a safe distance until it is safe to return to the blasting site.
The list above captures some of the major changes that employers should be aware of at a high level. The changes to the OHS Code are detailed and extensive, and they may have a significant effect on your workplace. Please contact a member of our Labour & Employment team if you would like to discuss these changes or their impact.
Note: This article is of a general nature only and is not exhaustive of all possible legal rights or remedies. In addition, laws may change over time and should be interpreted only in the context of particular circumstances such that these materials are not intended to be relied upon or taken as legal advice or opinion. Readers should consult a legal professional for specific advice in any particular situation.